Starters for synchronous and asynchronous motors
Available starting systems for electric motors:
- Electronic soft starter with thyristors up to 4 MVA motor output
- Starting transformers for synchronous an asynchronous motors up to 25 MW
- Liquid starters
Thanks to finely tuned soft start control, AEG electronic soft starters are gentle on motors and the unit to be driven.
AEG starting systems are used to avoid typical starting problems such as high current surges and high wear. AEG motors are available for mains voltages of 400, 500 and 690 V up to approx. 3000 A. The soft starters are looped into the motor connections. Typical areas of application are all non-speed-controlled drives, for example for conveyor belts, compressors, cooling systems and mixers, fans, mills, pumps and centrifuges. The starting devices with starting transformer for medium voltage up to 13.8 kV are designed according to “Korndorfer” three-switch method. The scope of delivery includes a complete unit with transformer, vacuum switches (neutral point and bypass contactor) and protective devices.
Our starters are supplied independently of the motor and switchgear manufacturers. They can be installed directly next to the motor or in the switchgear house. The transformers are supplied either as dry-type transformers or with oil cooling. For the design, we require a speed/torque curve, information on the motor current for direct connection and the mass moments of inertia. On request, we can also design low-cost liquid starters for your systems.
Classic DC drive technology like this is still widely used today. It is used in particular for modernizations and conversions in the steel industry. In the event that AEG IE is no longer able to supply the AEG Minisemi, Midisemi and Maxisemi products, suitable replacement products are available. The following picture shows the control cabinet of a large armature converter with 750V DC and 14,000 A DC in a 24-pulse version.
VSI invertors with constant voltage intermediate circuits with IGBT feeders for 4- quadrant (AFE) drives without line reactions
For multimotor drives a VSI invertor can be equipped with various motor inverters and a controlled DC bus provided. From the supplying grid only the total of active power is drawn in this case. In plants frequently only some motors are operating motorically, others are feeders. The feeding drives (which are braking) across the DC bus are supplying energy to the driving motors. This is an optimal energy concept.
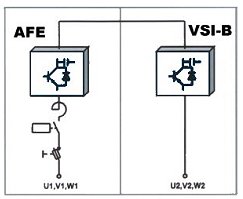
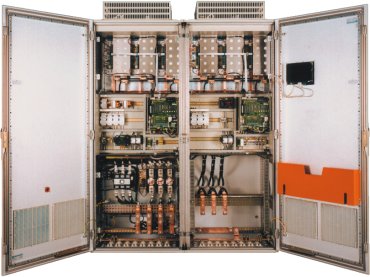

BL-Motor- Inverter with constant current intermediate circuits for synchronous motors
The BL-drive is specially suitable for large driven units with only one direction, e.g. pumps, fans and compressors. It is also in use as starting inverter in power stations.
output range | approx. 1 to 50 MW |
speed range | up to max 6000 rpm |
cooling | air and water |
Further information on the BL drive system is available as pdf-document.
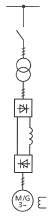
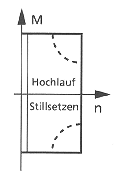
Modernizing and backfitting
Aus Erfahrung gut. AEG IE draws on years of experience in the field of drive modernization. Our proven know-how is particularly in demand in the following specialist areas:
- Revamping of inverters for speed controls of pumps and fans for economizing energy and reduction of losses in power stations and other industrial plants
- Modernizing of DC drives in steel plants or mines
The following picture shows the mounting of a water cooled inverter in a container cubicle and its installation in a machine hall of a power station in Italy. It was an order for four feed water pumps with 2,1 MW each in a container of 5 by 3 by 3 meters with a complete inverter and insulated direct water cooling for each drive.
AEG IE modernizes not only AEG power converters, but also used products from other manufacturers in Western and Eastern Europe. AEG IE integrates parts of the systems that can still be used into the new solution. The modernization of old medium and high power DC drives is often of great economic interest. These are often drives in rolling mills, cement works, conveyors and crane systems. The new, fully digital information electronics can also be used for very dynamic drives. Existing DC motors can be inspected and overhauled if necessary. Our motor factory can supply new motors if required.
When modernizing power converters, it sometimes makes sense to continue using the thyristor power components. In such cases, we supply a customer-specific interface with the new digital controller to adapt to the given situation in the power section. The new control system has connections to common bus systems (Profibus-DP, CAN) for communication with the higher-level automation level. The new control electronics have a flexibly combinable drive structure with a range of technology modules, hierarchical controls and a fault memory.
If new power units are required, we can make appropriate offers.
Drives and thyristorized equipment with highly dynamic properties
Especially for test benches of the automobile industry we can offer suitable speed controlled drives. Our offer includes the semiconductor equipment, motors with rotors of low rotating masses and intelligent interfaces for primary automation modules. We avail of considerable experience with motor and gearbox test benches as well as car test benches and for other related uses.

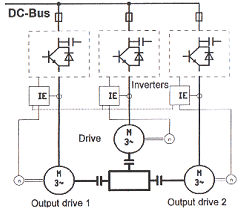
Characteristics
Output range 10 to 4000kW
- Feeder 400 to 690V
- Line frequency 50 or 60 cycles
- Line re-feeder by pulses
- Torque control reaction time < 1,5ms
- Speed control range with speedometer 1:1000
- High synchronism at low rpm
- Field control > 1:5
- Refrigeration by air or water
- Protection type IP23 und IP54
- EMV acc. to IEC 801-2...4
Other applications upon request.
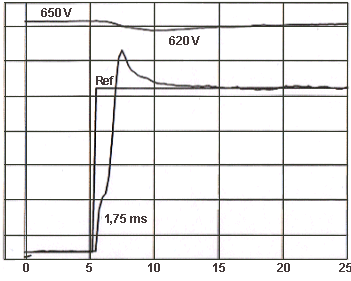
Drives for conveyor belts
Speed-controlled drives for belt conveyors and conveyor systems are recommended due to the following advantages. AEG IE advises, designs and supplies:
- Instead of slipring motors, squirrel cage motors should be used
- The resistance controller in the rotor circuit may be omitted
- A complete reserve drive for revision purposes can be omitted
- A lower, more economic belt configuration can be selected
- The losses are considerably lower
- The maintenance cost can be reduced, lesser failure and breakdown times
- Roller, belt and gear are subject to lower wear rate
If existing conveyor belts are equipped with speed controls and the slipring motor shall be retained, we can offer an electronic speed control with a subsynchronous thyristorized cascade (USK).
An essay on the above mentioned plant with three phase squirrel cage motors regulated by speed controlled inverters is available as pdf.